Cuando hablamos de Industria 4.0 nos referimos a la tecnología de la automatización que pone a nuestra disposición una gran cantidad de datos, la cual nos permite conocer el estado de las máquinas en las diferentes cadenas de procesos dentro de cualquier fábrica. Todo esto se traduce en empresas que producen bienes de mayor calidad a un menor coste.
Las herramientas son los elementos clave de esta cuarta revolución, por lo que tenemos que contar con los mejores proveedores de productos y servicios, y así evitar cualquier fallo que se pueda producir.
Si bien es cierto que muchas empresas siguen apostando por la monitorización de condición in situ, hoy en día hay muchos activos que ofrecen la posibilidad de realizar los análisis de forma automática y remota, lo que permite conocer el estado de la máquina en tiempo real, independientemente del lugar dónde se encuentre el técnico. Este sistema no solo alerta a los responsables de los activos afectados en el caso de producirse cualquier tipo de anomalía, sino que también se realizan análisis continuos y crean relaciones entre los datos históricos y las lecturas actuales. Este nuevo método de mantenimiento reduce drásticamente el número de intervenciones que realiza el equipo técnico de forma reactiva para solucionar cualquier problema que el equipo tuviese.
La tecnología que se utiliza para gestionar toda esta cantidad de información es el Machine Learning e Inteligencia Artificial, permitiendo que el algoritmo identifique automáticamente posibles paradas no programadas, haga recomendaciones sobre tareas de mantenimiento óptimas para cada tipo de problema y, en general, minimice el tiempo de inactividad de una planta.
Como definición, el Machine Learning es la aplicación actual de la Inteligencia Artificial donde las máquinas tienen acceso a datos, aprenden y mejoran automáticamente de la experiencia sin estar explícitamente programadas, ya que está continuamente observando lo que está sucediendo y cuál es el resultado.
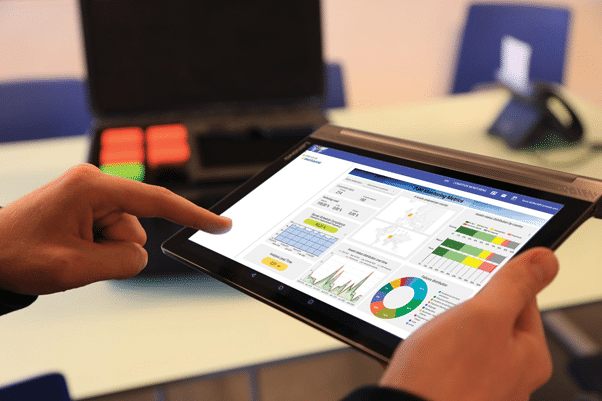
El mantenimiento predictivo se puede aplicar en una variedad muy amplia de contextos y ofrece importantes beneficios. En un estudio de la conocida consultora PwC se baraja que, una correcta aplicación de un plan de mantenimiento predictivo, puede:
– Reducir hasta un 12% de los costes
– Aumentar el tiempo de actividad de la fábrica en un 9%
– Reducir el riesgo de accidentes laborales en un 14%
– Incrementar la vida útil de un equipo hasta un 20%
Este tipo de ventajas hace que nos preguntemos: si nos podemos anticipar a un problema, ¿es realmente un problema?
Los líderes de fabricación ya están comenzando a ver el mantenimiento predictivo no como un gasto sino como una inversión en sus plantas, además de comprender la importancia de utilizar estas técnicas predictivas junto a la Inteligencia Artificial para la monitorización de activos costosos y complejos. Es momento de dejar paso al mantenimiento 4.0 y confiar en los avances tecnológicos para evitar cualquier tipo de anomalía que afecte negativamente al proceso de producción de la empresa.